Powder metallurgy is a technology that uses metallic powders (or mixtures of metallic and non-metallic powders) as raw materials to produce metallic materials, composites and various types of products after forming and sintering. Powder metallurgy methods are somewhat similar to the production of ceramics; therefore, a range of new powder metallurgy techniques are also available for the preparation of ceramic materials. Due to the advantages of powder metallurgy technology, it has become the key to solving new material problems and plays a key role in the development of new materials.
Many factors affect the properties of sintered bodies, namely the powder properties, forming and sintering conditions. Factors in the sintering conditions include heating rate, sintering temperature and time, cooling rate, sintering atmosphere and pressure conditions.
Sintering temperature and time
Sintering temperature and duration can affect the porosity, density, strength and hardness of the sintered body. High sintering temperatures and long heating times can degrade product performance and even lead to scorch defects, while low sintering temperatures or long heating times may lead to degraded performance due to the sintering process.
Sintering atmosphere
Sintering atmospheres commonly used in powder metallurgy are reducing atmospheres, vacuums, hydrogen atmospheres, etc. The sintering atmosphere has a direct influence on the properties of the sintered body. The sintering atmosphere directly affects the properties of the sintered body. Sintering in a reducing atmosphere prevents the burning of the briquettes and allows the reduction of surface oxides. For example, iron and copper based products are usually decomposed using gas or ammonia, while carbide and stainless steel are usually made with pure hydrogen. Reactive or refractory metals (e.g. beryllium, titanium, zirconium, tantalum), carbide alloys containing Tic and stainless steel can be vacuum sintered. Vacuum sintering avoids harmful components (H2O, O2).
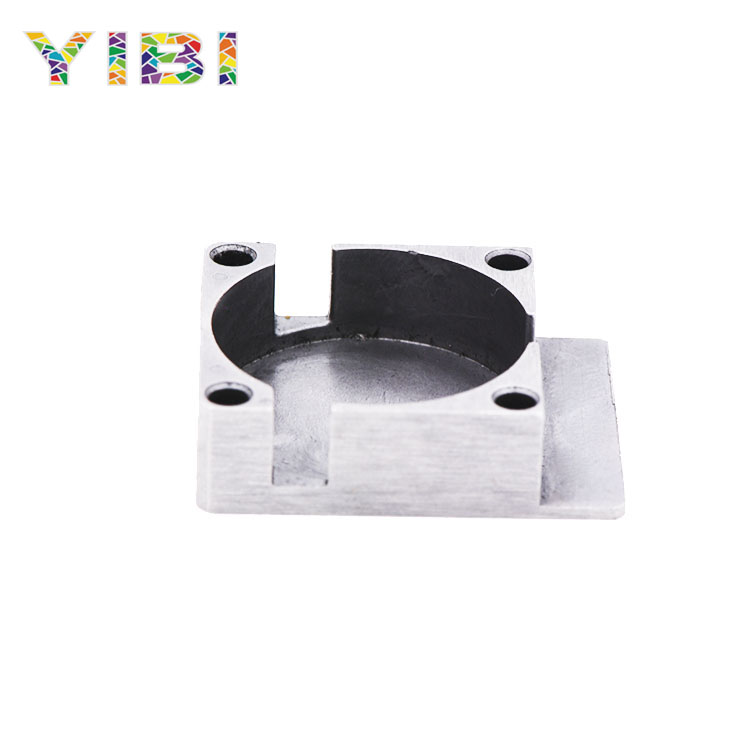
Powder metallurgy sintering method
Liquid Phase Sintering
If two or more components are present in the powder briquettes, sintering may occur above the melting point of the components, resulting in a small amount of liquid phase in the powder briquettes.
Pressure sintering
Pressure is applied to the powder during sintering to facilitate the densification process. Sometimes pressure sintering and hot pressing are synonymous, but hot pressing refers to the process of forming and sintering the powder to obtain a product directly after sintering.
Activated sintering
It is also a way to improve the performance of the sintered body while using some physical or chemical measures to significantly reduce the sintering temperature and reduce the sintering time.
Spark sintering
When the powder is introduced into the compaction process, direct current (DC) and pulsed power is then used to create an arc between the powder particles. The sintering process then begins. During the sintering process, pressure is gradually added to the workpiece, thus combining the forming and sintering of both processes.